DIE CASTING
Quality DIE CASTING Service
Aluminum die casting is a manufacturing process where molten aluminum (or aluminum alloys) is forced under high pressure into a steel mold or die to produce complex, precise, and durable components. This method is widely used in various industries, including automotive, aerospace, electronics, and consumer goods, because of its efficiency and the excellent material properties of aluminum.
Process of Aluminum Die Casting
Die Preparation:
- The steel mold is cleaned, lubricated, and pre-heated.
Injection:
- Molten aluminum is injected into the mold cavity under high pressure.
Cooling:
- The aluminum solidifies quickly within the die.
Ejection:
- The part is ejected from the mold.
Trimming:
Excess material (like gates or runners) is removed from the cast part.
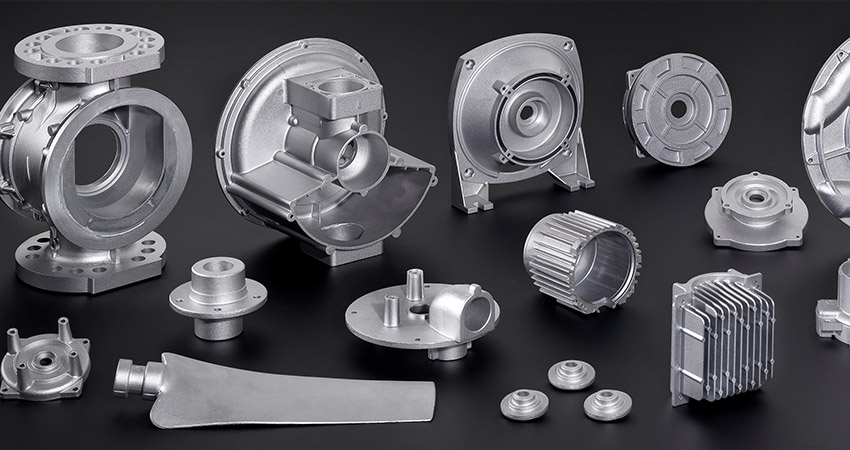
